La producción de radios de alta calidad fue una seña de identidad de la empresa en sus comienzos. DT era sinónimo de radios suizos de calidad superior incluso antes del nacimiento de la actual DT Swiss AG. A día de hoy, los radios DT Swiss representan durabilidad y precisión y son imbatibles gracias a su proceso de producción exclusivo, que combina ligereza con durabilidad.
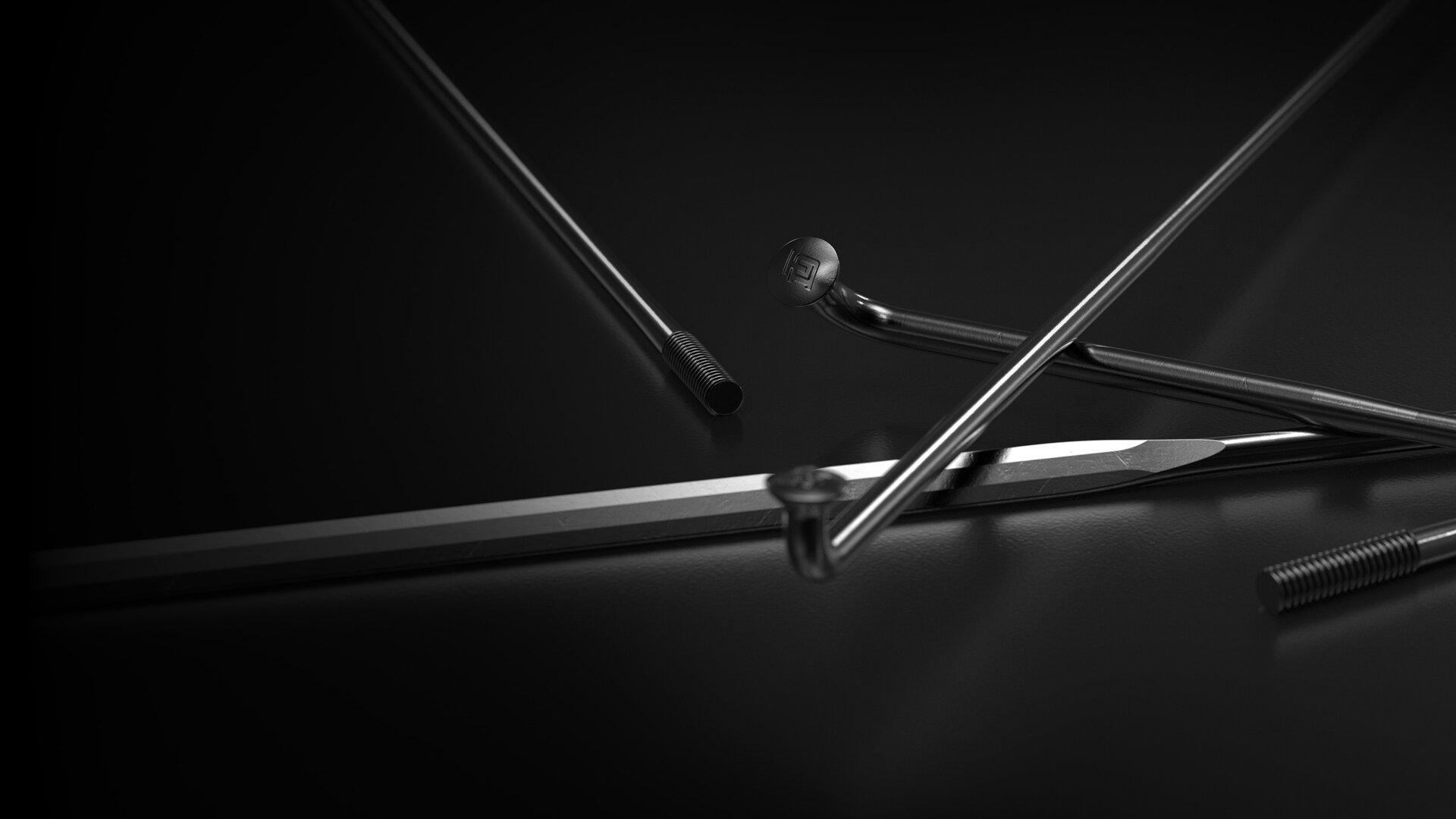
TECNOLOGÍA de
radios
Cómo producimos tus radios, paso a paso
Materia prima de acero
La aleación de acero que empleamos está tratada especialmente para la fabricación de radios y proviene de proveedores de alambre seleccionados. Esta materia prima tiene que ser de una calidad elevada y homogénea, y se somete a controles sistemáticos.
Los radios se someten a toda una diversidad de alteraciones, por lo que una aleación de acero específica permite procesar el alambre hasta conseguir las propiedades requeridas de resistencia y elongación del alambre para radios. Desde este punto, el control de calidad es esencial: la materia prima que recibimos debe satisfacer las exigencias de DT Swiss tanto en su composición como en su calidad.
El alambre como materia prima
El alambre para radios de acero inoxidable 18/10 suministrado ya se ha sometido a ensayos de flexión y tracción antes de salir del proveedor. El alambre para radios se enrolla en carretes (bobina) de unos 800-900 kg y nos llega en 4 diámetros diferentes: 1.8, 2.0, 2.15 y 2.34 mm. La directa comunicación y coordinación del control del producto entre DT Swiss y el proveedor del alambre garantizan el cumplimiento de nuestras estrictas tolerancias de acabado superficial, diámetro y ovalidad del alambre. Solo cumpliendo estas especificaciones es posible garantizar una producción de radios eficiente y compatible con las máquinas de proceso. La inspección por parte del proveedor antes de salir de su planta es idéntica a la inspección de entrada que aplica DT Swiss. Para garantizar una superficie lisa, las pruebas se basan en el simple contacto con la mano en la superficie de la bobina. A continuación, se comprueban el diámetro y la ovalidad con un micrómetro.
Enderezado de los radios
El alambre se desenrolla directamente de las bobinas, se endereza en una máquina y se corta a la medida para formar los radios en bruto. Este paso se realiza con todos los radios y da como resultado radios rectos y cortados con una precisión de centésimas. En esta etapa, el control más importante no se hace solo en el material, sino también en la máquina y su desgaste. Cada máquina de la producción se verifica dos veces al día con diferentes herramientas de medición que aplican unas tolerancias estrictas para garantizar una calidad y un acabado constantes en el material. Este control es muy importante para que los pasos de procesamiento posteriores funcionen a la perfección.
Forja en frío
Este proceso, desarrollado y patentado por DT Swiss, se utiliza para reducir el diámetro de los radios hasta la medida deseada. Mediante la rotación de martillos oscilantes alrededor del alambre, el radio en bruto se comprime y se reduce su diámetro. Este proceso da como resultado un radio a la vez ligero y resistente, con una parte elástica conificada para una mayor ligereza y una cabecilla y rosca más firmes para una mayor capacidad de carga.
Gracias al proceso de forja en frío, el material gana resistencia, pero conservando sus buenas propiedades de alargamiento. La transición del diámetro reducido al no reducido de un radio es tremendamente armoniosa y resulta en un aspecto de alta calidad. Antes del siguiente paso, se comprueba a mano la rectitud, el diámetro y la ovalidad de una muestra de radios.
Formación de la cabecilla y la rosca
A medida que avanzan los pasos, el producto se acerca más a una forma reconocible. Los radios se cortan a una dimensión exactamente calculada y deseada. Inmediatamente después, se estampa la cabecilla, a la que se incorpora el exclusivo símbolo «DT». Los radios clásicos reciben además su ángulo de 90-95°. En el otro extremo del radio en bruto, se forma la rosca mediante un proceso de laminado que garantiza la longitud correcta y la forma en J de los radios Classic, y fortalece al mismo tiempo el material de la rosca, algo que simplifica la construcción de la rueda y aumenta su resistencia.
En este punto, los radios se someten a distintos controles. Una inspección visual de la cabecilla verifica que esté presente el logotipo y que el material no muestre defectos en cuanto al ángulo. El diámetro de la cabecilla, la longitud del ángulo y la rosca (longitud y diámetro) se miden con un calibre digital. La rosca del radio se somete a una prueba de funcionamiento manual. La última medición es una medición del punto cero con el altímetro Trimons. Esta serie de pruebas se realiza cada 35 minutos en al menos un radio.
Forja en plano
El material de partida son radios de espesor continuo o forjados en frío, los cuales se aplanan durante este proceso con un peso de hasta 200 toneladas. Gracias a esta forma plana, el radio proporciona ventajas especialmente aerodinámicas. Este proceso de forja adicional densifica aún más el material, lo que a su vez consigue más resistencia. Se comprueban la longitud y la parte plana de cada radio, en un control de calidad que tiene lugar cada 15 minutos.
Pavonado de los radios
Por razones estéticas, los radios también se pueden pavonar. Aunque parece sencillo, este proceso de pavonado es bastante específico para garantizar que la coloración de los radios no añada peso ni suponga pérdidas de rendimiento. En cada pedido, se comprueba la calidad del pavonado en una muestra de radios para garantizar una resistencia óptima incluso después de varios años. Alrededor del 85 % de los radios que salen de fábrica son negros.